Turning Challenges into Opportunities: Turbine Rotor Repair Solutions for Enhanced Performance
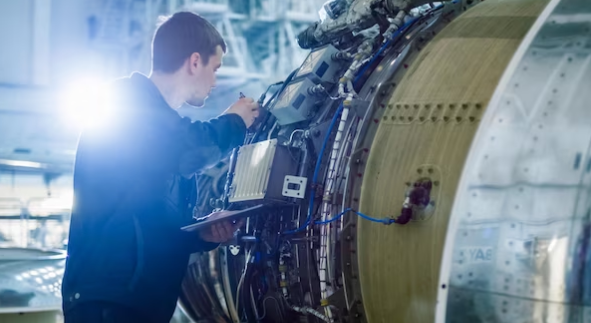
The efficient functioning of turbines is crucial for power generation, and the rotor stands as a critical component in this process. Over time, turbine rotors may face wear and tear, presenting challenges that, when addressed strategically, can become opportunities for enhanced performance. In this comprehensive article, we explore the challenges associated with turbine rotor repair and delve into innovative solutions that not only rectify issues but also elevate the overall performance of the turbine.
Challenges in Turbine Rotor Repair
Turbine rotor repair is a complex and critical aspect of maintaining efficient power generation systems. The challenges associated with this process require careful consideration and innovative solutions to ensure the continued reliability and performance of turbines. In this section, we will delve into the multifaceted challenges encountered during turbine rotor repair and discuss the implications they have on the overall operation of power plants.
1. Wear and Fatigue:
Turbine rotors, subjected to the rigors of high-speed rotation and constant operational stress, are prone to wear and fatigue over time. The continuous exposure to extreme temperatures and pressures contributes to material degradation, impacting the rotor’s efficiency and structural integrity.
Implications:
- Reduced turbine efficiency leading to lower power output.
- Increased vibrations, potentially affecting other components.
- Higher risk of catastrophic failure if wear and fatigue are not addressed promptly.
2. Blade Erosion:
The high rotational speeds of turbine blades make them susceptible to erosion caused by abrasive particles in the working fluid. This erosion can compromise the aerodynamic profile of the blades, diminishing their efficiency in converting fluid energy into mechanical energy.
Implications:
- Decreased power output due to reduced aerodynamic efficiency.
- Higher maintenance costs associated with frequent blade replacements.
- Imbalance issues that can affect the entire turbine system.
3. Cracks and Structural Damage:
Turbine rotors undergo thermal cycling and experience operational stresses, leading to the development of cracks and structural damage. These issues can compromise the overall structural integrity of the rotor, posing serious challenges for maintenance teams.
Implications:
- Increased risk of rotor failure if cracks are not addressed promptly.
- Compromised safety and the potential for environmental hazards.
- The need for frequent and extensive repairs, impacting operational downtime.
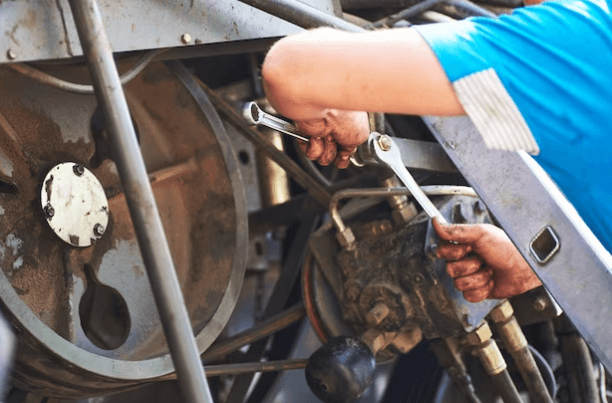
Innovative Solutions for Turbine Rotor Repair
In the ever-evolving landscape of power generation, turbine rotor repair has become a focal point for innovation. Addressing challenges in turbine maintenance requires not only effective solutions but also forward-thinking approaches that elevate efficiency and reliability. This section delves into cutting-edge strategies and technologies, showcasing the innovative solutions that are shaping the future of turbine rotor repair.
1. Advanced Coating Technologies:
The application of advanced coatings, particularly thermal barrier coatings (TBCs), marks a significant advancement in turbine rotor repair. TBCs act as a shield, providing resilience against the harsh operational conditions characterized by high temperatures and corrosive elements. These coatings not only protect turbine components but also extend their lifespan, contributing to sustained efficiency and performance.
Benefits:
- Extended Component Lifespan: TBCs offer prolonged protection, reducing the frequency of repairs and replacements.
- Enhanced Performance: Improved resistance to wear and corrosion results in heightened operational efficiency.
2. Precision Repairs and Refurbishment:
Embracing precision machining techniques signifies a shift towards engineering precision in turbine rotor repair. This approach focuses on the meticulous restoration of aerodynamic profiles, eliminating imperfections that may lead to vibrations or reduced efficiency. Leveraging cutting-edge machining technologies allows maintenance teams to achieve unparalleled accuracy in refurbishing turbine components.
Benefits:
- Vibration Reduction: Precision repairs lead to smoother surfaces, minimizing vibrations and ensuring the optimal rotational balance of the rotor.
- Efficiency Optimization: Restoring aerodynamic profiles to their original specifications enhances energy conversion efficiency, boosting overall turbine performance.
3. Non-Destructive Testing (NDT) Methods:
Incorporating advanced NDT methods, including ultrasonic and magnetic particle testing, represents a proactive stance in turbine rotor maintenance. These non-invasive techniques enable comprehensive inspections without causing damage to components. Early detection of flaws or irregularities empowers maintenance teams to intervene promptly, mitigating potential issues.
Benefits:
- Early Flaw Detection: NDT methods identify potential problems in their infancy, preventing unexpected failures and minimizing downtime.
- Preservation of Structural Integrity: Thorough inspections contribute to maintaining the structural integrity of turbine rotors, ensuring long-term reliability.
Read also The Evolution of Lighting Design: Past, Present, and Future
4. Thermographic Monitoring Systems:
The integration of thermographic monitoring systems introduces a real-time dimension to turbine rotor health assessment. By continuously monitoring temperature distribution across the rotor, these systems offer insights into potential hotspots or areas of concern, allowing for timely preventive measures.
Benefits:
- Proactive Maintenance: Early identification of hotspots enables timely intervention, preventing overheating and potential damage.
- Enhanced Safety: Thermographic monitoring contributes to a safer operating environment by minimizing the risk of thermal-related incidents.
The Future of Turbine Rotor Repair: Emerging Technologies
As the energy landscape continues to evolve, new technologies are poised to revolutionize turbine rotor repair, further enhancing efficiency and reliability.
1. Additive Manufacturing (3D Printing):
The adoption of additive manufacturing, specifically 3D printing, signifies a paradigm shift in turbine rotor repair. This technology allows for the production of intricate components with customized designs. It enables the creation of complex geometries that were previously challenging or impossible to manufacture using traditional methods.
Potential Benefits:
- Customization: 3D printing enables the creation of tailor-made components, optimizing performance based on specific operational requirements.
- Efficient Production: Reduced lead times and material wastage contribute to more efficient and sustainable turbine rotor repair processes.
2. Smart Sensors and Condition Monitoring:
The increasing use of smart sensors for real-time monitoring of turbine rotor health heralds a new era in predictive maintenance. These sensors continuously collect data on various parameters, providing insights into the performance and condition of the rotor. This data-driven approach allows for proactive maintenance planning, reducing downtime and enhancing overall reliability.
Potential Benefits:
- Predictive Maintenance: Smart sensors enable the prediction of potential issues, allowing for timely interventions and minimizing unexpected failures.
- Data-Driven Decision Making: Continuous monitoring provides a wealth of data for informed decision-making, optimizing maintenance strategies.
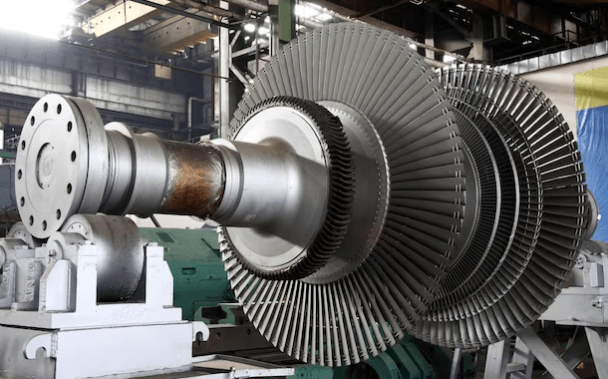
Case Studies: Successful Implementation of Turbine Rotor Repair Solutions
Through strategic application of precision repairs and advanced coating technologies, turbine rotor efficiency was restored, leading to prolonged operational life and minimized downtime.
1. Renovation of a Gas Turbine Rotor:
- Challenge: Severe blade erosion and wear.
- Solution: Application of erosion-resistant coatings, precision machining, and aerodynamic profile restoration.
- Outcome: Restored efficiency, extended rotor lifespan, and improved power output.
2. Crack Remediation in a Steam Turbine Rotor:
- Challenge: Cracks and structural damage.
- Solution: Advanced NDT methods for crack detection, followed by precision welding and structural reinforcement.
- Outcome: Enhanced structural integrity, minimized risk of failure, and prolonged operational life.
Conclusion
In the realm of turbine rotor repair, challenges can indeed be turned into opportunities for improved performance. Through the strategic application of advanced coating technologies, precision repairs, innovative testing methods, and the incorporation of emerging technologies, the efficiency and reliability of turbine rotors can be significantly enhanced. By exploring case studies that showcase successful implementations and looking ahead to future trends, this article underscores the importance of proactive maintenance in the dynamic field of power generation. As the industry continues to evolve, turbine rotor repair solutions will play a pivotal role in shaping the future of efficient and sustainable energy production.