Why Precise Timer Settings Matter in Powder Coating Ovens for Consistency
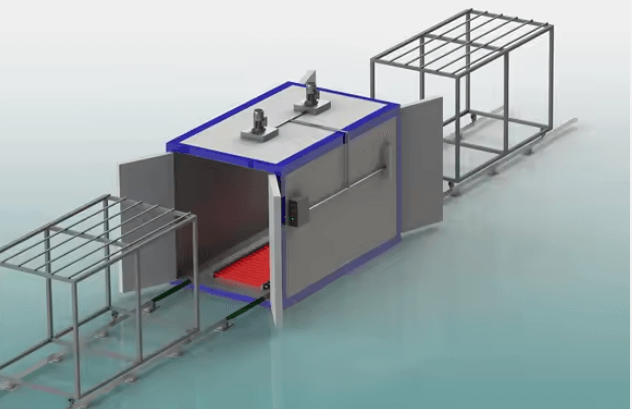
Timing is everything, especially when it comes to achieving flawless results in powder coating. The performance of powder coating ovens hinges on accurate timer settings to ensure each layer cures properly. When timing is off, even by a small margin, the outcome can range from minor defects to full-on failures. Let’s dive into why precision timing is vital and how it impacts the overall quality and durability of your coated products.
Fluctuating Coating Thickness Leading to Weakened Protection
Timing inaccuracies in powder coating ovens can directly influence the thickness of the coating. When parts are left in the oven for too long or not long enough, the powder may fail to evenly melt and cure. This inconsistency creates variations in coating thickness, which compromises the surface’s ability to provide adequate protection.
Thicker sections might result in brittle coatings that crack under stress, while thinner areas may leave the surface vulnerable to corrosion, wear, or impact damage. A quality powder coating oven with precise timer settings helps maintain uniform heat distribution, ensuring the coating adheres consistently. By eliminating guesswork, these ovens provide the level of precision needed to protect your parts without compromising their structural integrity.
Inconsistent thickness doesn’t just affect durability—it can also impact aesthetics. Uneven finishes look unprofessional, undermining the product’s value. Reliable powder coating ovens with calibrated timers help ensure your results remain as visually appealing as they are functional.
See also: The Tech Behind Fast Payout Casinos: How Blockchain and AI Are Speeding Up Transactions
Loss of Adhesion Compromising Long-Term Performance
Adhesion is the cornerstone of a high-performing powder coating. Without proper adhesion, the coating may peel, flake, or chip over time, rendering it ineffective. Incorrect timer settings in your powder coating oven can significantly impact this process, leaving you with coatings that simply don’t stick.
Under-curing occurs when the coating doesn’t reach the necessary temperature for the required duration. This prevents the powder from fully bonding with the surface, leading to poor adhesion. On the flip side, over-curing can also cause problems, as excessive heat can weaken the bond between the coating and the substrate. Finding the sweet spot requires precise timing, which reliable powder coating ovens are designed to provide.
Adhesion failures can result in costly rework and damage to your reputation. Properly calibrated ovens ensure that each batch meets exact curing requirements, helping you avoid these pitfalls and delivering long-lasting, high-quality results.
Blistering and Cracking Due to Overexposure to Heat
One of the most common issues caused by poor timer management is blistering or cracking in the coating. These defects are usually the result of overexposure to heat during the curing process. Even slight deviations from recommended curing times can cause the powder to degrade, leading to surface imperfections.
Blisters often form when trapped air or moisture expands under excessive heat, creating unsightly bubbles. Cracking, on the other hand, happens when the coating becomes overly brittle due to prolonged exposure. Both issues not only detract from the appearance of the finish but also compromise its protective capabilities.
By using a quality powder coating oven with accurate timer settings, you can mitigate these risks. Compact powder coating ovens equipped with modern control systems allow you to fine-tune curing times, ensuring that each part receives just the right amount of heat for an optimal finish.
Subtle Color Variations Creating an Inconsistent Finish
In industries where aesthetics are critical, even the smallest color variation can stand out. Improper timing during the curing process can cause subtle but noticeable differences in color, particularly in large batches of parts. These variations can occur because different areas of the coating react differently to uneven heating or curing times.
For example, under-cured coatings may appear dull or patchy, while over-cured sections can take on a burnt or discolored look. These inconsistencies are especially problematic when matching specific color standards or brand requirements. A reliable powder coating oven with precise controls helps eliminate these issues by ensuring every piece cures evenly.
When your oven maintains consistent timing across all parts, you not only improve the visual appeal but also reinforce the quality of your brand. Customers notice when finishes look polished and uniform, making accurate timer settings an essential part of the process.
Brittle Surfaces That Fail Under Stress or Impact
Brittleness is another issue that stems from incorrect timing in powder coating ovens. Over-curing can make the coating excessively hard, reducing its flexibility and ability to withstand impact. This can be disastrous for parts that need to perform under stress, such as machinery components or outdoor fixtures.
Properly set timers ensure the coating cures to the ideal level of hardness and elasticity. This balance is crucial for applications requiring durability and long-term performance. With compact powder coating ovens designed for precision, you can avoid the pitfalls of over-curing and produce parts that stand up to real-world conditions.
Reliable timing also extends the lifespan of the coating. Brittle surfaces are more likely to crack or chip over time, but a properly cured finish remains intact even under demanding circumstances.
Increased Rework and Scrap Costs from Defective Batches
Defective batches caused by poor timing can quickly add up in terms of wasted resources and labor. Reworking parts isn’t just time-consuming—it’s also expensive. In some cases, defects may render parts completely unusable, leading to additional costs for replacements or scrap.
Accurate timer settings in your powder coating oven can drastically reduce these risks. By ensuring each batch is cured correctly the first time, you minimize waste and increase efficiency. Quality powder coating ovens are designed with this level of precision in mind, helping you maintain consistent results and lower operational costs.
Investing in a reliable oven with advanced timer controls isn’t just about avoiding defects—it’s about optimizing your entire process. With fewer issues to address post-curing, your team can focus on what matters most: delivering high-quality products to your customers.