The Future of Manufacturing: How SLA/DLP Resins Are Changing the Game
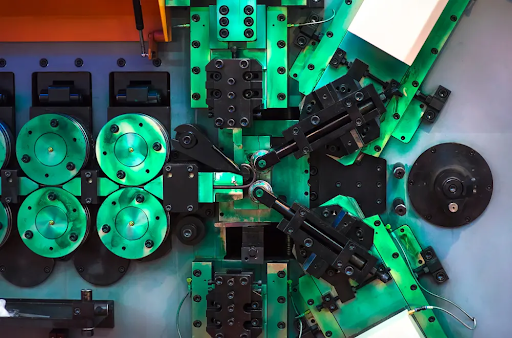
For years, 3D printing was seen as a tool for rapid prototyping—useful, but not quite ready for full-scale production. That perception is changing, fast. Thanks to major advancements in resin 3d printing-based additive manufacturing, technologies like Stereolithography (SLA) and Digital Light Processing (DLP) are now producing high-performance, end-use parts across industries. From aerospace to healthcare, these materials are proving they can stand toe-to-toe with traditional thermoplastics.
So, what makes SLA and DLP so revolutionary?
Precision Meets Performance
One of the biggest advantages of SLA and DLP printing is the unmatched precision they offer. Traditional methods like Fused Deposition Modeling (FDM) leave visible layer lines and can struggle with fine details. SLA and DLP, on the other hand, use photopolymer resins to achieve resolutions as fine as 25 microns, delivering smooth, injection-mold-quality finishes with minimal post-processing.
But precision alone isn’t enough—these parts need to be strong, durable, and reliable. Early SLA/DLP resins were brittle, limiting their use to prototypes. Today, high-performance photopolymers rival materials like ABS, polyamide (PA12), and polypropylene (PP) in both strength and flexibility.
Breaking the Stigma: Resins That Rival Thermoplastics
For a long time, resin-based 3D printing had a reputation for fragile, short-lived parts. That’s no longer the case. Modern SLA/DLP resins are engineered to provide:
✅ High Toughness & Impact Resistance – Some resins now achieve elongation-at-break values exceeding 100%, making them flexible and durable.
✅ Heat Resistance Over 300°C – High-temperature resins allow applications in aerospace, automotive, and industrial tooling.
✅ Wear-Resistant Ceramic Composites – Ideal for manufacturing jigs, fixtures, and mold masters.
✅ Biocompatibility & Medical-Grade Properties – Certified resins now enable production of surgical guides, prosthetics, and even soft tissue simulation models.
Thanks to these advancements, SLA and DLP are no longer just for concept models—they’re now key players in end-use manufacturing.
Why Businesses Are Switching to SLA/DLP
Manufacturers are increasingly turning to SLA and DLP for low-to-mid-volume production runs. Why? Because these technologies offer:
🔹 Faster Print Speeds – DLP’s area-wide exposure system outpaces traditional layer-by-layer methods, making it one of the fastest 3D printing technologies available.
🔹 Rapid Material Swaps – Unlike powder-based systems, which require hours of cleaning and sieving, SLA/DLP resins can be swapped in minutes.
🔹 Lower Material Waste – Unlike Selective Laser Sintering (SLS), where unused powder must be recycled, SLA/DLP uses liquid resins efficiently with minimal waste.
🔹 Simplified Post-Processing – No extensive depowdering, mechanical removal, or complex post-cure treatments—just wash, cure, and go.
The result? A more agile and cost-effective alternative to traditional manufacturing methods.
Real-World Applications: Where SLA/DLP Shines
🚀 Aerospace & Automotive – High-temperature, flame-retardant resins are now compliant with UL94 V-0 and Airbus AITM standards, making them ideal for interior components, ducts, and brackets.
🏥 Medical & Dental – Biocompatible resins certified under ISO 10993-5 & -10 support the production of custom surgical guides, dental prosthetics, and anatomical models.
🏭 Industrial Manufacturing – Wear-resistant ceramic-filled resins are replacing traditional tooling materials in jigs, fixtures, and injection mold prototypes.
From custom car parts to patient-specific medical devices, SLA/DLP is delivering high-performance solutions where precision and material versatility matter most.
The Future of SLA/DLP: A Manufacturing Revolution
With continued advancements in resin chemistry, print speed, and automation, SLA/DLP is poised to become a dominant force in modern manufacturing. As Industry 4.0 pushes businesses toward on-demand production and mass customization, resin-based 3D printing offers the flexibility, efficiency, and material diversity needed to keep up.
If your business isn’t already exploring SLA/DLP, the question isn’t if—it’s when.
Transform Your Manufacturing Process Today
The future of production is here, and SLA/DLP is leading the way. Whether you’re looking to enhance precision, speed, or material versatility, resin-based 3D printing offers a game-changing solution.
🚀 Don’t get left behind—discover how SLA/DLP can revolutionize your manufacturing.