What Does Thermoformer Mean? A Comprehensive Guide
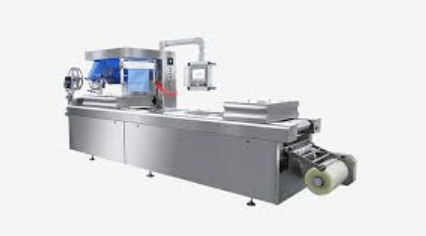
Thermoforming is a versatile manufacturing process that plays a crucial role in the production of a wide range of products, from packaging materials to automotive components. In our comprehensive guide, we’ll explore the world of thermoforming, diving into its definition, the process, and the different uses across various industries.
Understanding Thermoforming
Thermoforming is a manufacturing process that involves heating a plastic sheet until it becomes pliable, forming it into a specific shape using a mold, and then cooling it to create a rigid, usable product. The term “thermoformer” refers to the machinery used in this process, as well as the professionals skilled in executing it.
The Thermoforming Process
Heating
Thermoforming begins with the heating of a plastic sheet until it reaches a pliable state. This can be achieved through various methods, including infrared heaters, convection ovens, or contact heating.
Forming
The heated sheet is then placed over a mold, and a vacuum or pressure is applied to force the material into the desired shape. This step is crucial for achieving precision in the final product.
Cooling
After forming, the plastic is cooled to solidify and maintain its shape. This can be done using fans, water sprays, or other cooling methods.
Trimming
Excess material is trimmed away, leaving behind the finished product. This step ensures that the final piece meets the design specifications.
Applications of Thermoforming
Packaging
Thermoforming is widely used in the packaging industry to create containers, trays, and blister packs. Its ability to produce custom shapes and sizes makes it an ideal choice for packaging solutions that require both functionality and visual appeal.
Automotive Industry
From interior components like dashboards and door panels to exterior parts such as vehicle body panels, thermoforming is integral to the production of various automotive components. Its cost-effectiveness and lightweight nature contribute to its popularity in this industry.
Consumer Goods
Thermoforming is employed in the manufacturing of numerous consumer goods, including toys, electronic enclosures, and household items. The process allows for the creation of durable and aesthetically pleasing products.
Medical Devices
The medical industry relies on thermoforming for the production of sterile and disposable medical packaging trays and enclosures. The ability to create custom shapes and sizes is particularly advantageous in this field.
Advantages of Thermoforming
Thermoforming offers a range of advantages that make it a popular choice for the manufacturing of various products across industries. Here are some key advantages of thermoforming:
Cost Effective
Thermoforming is often more cost-effective than alternative manufacturing processes, such as injection molding or blow molding. The relatively low tooling costs and faster production cycles contribute to overall cost savings, making it an attractive option for large-scale manufacturing.
Design Flexibility
Thermoforming allows for a high degree of design flexibility. Complex shapes, intricate details, and custom geometries can be easily achieved, giving designers the freedom to create innovative and aesthetically pleasing products.
Rapid Prototyping
The process enables quick and cost-effective prototyping. This is especially beneficial during the product development phase, allowing designers to test and iterate designs before committing to full-scale production.
Fast Production Cycles
Thermoforming typically has shorter production cycles compared to other manufacturing methods. This quick turnaround is advantageous in meeting tight deadlines and responding promptly to market demands.
Material Variety
Thermoforming is compatible with a wide range of thermoplastic materials, offering versatility in terms of material properties. This includes different colors, textures, and material strengths, allowing manufacturers to choose the most suitable material for specific applications.
Reduced Waste
The thermoforming process generates less material waste compared to traditional subtractive manufacturing methods. Material efficiency is enhanced as the plastic sheet is molded directly into the desired shape, minimizing excess material that needs to be discarded.
Lightweight Products
Thermoformed products are inherently lightweight, making them ideal for applications where weight is a critical factor, such as in the automotive and aerospace industries. This characteristic contributes to fuel efficiency and ease of handling.
Scalability
Thermoforming is easily scalable for both small and large production runs. Whether producing a few prototypes or mass-producing throughs of units, the process is adaptable to varying production volumes.
Ease of Tooling
The tooling required for thermoforming is generally less complex and more cost-effective compared to other molding processes. This simplicity in tooling design contributes to faster setup times and cost savings.
Durable Products
Thermoformed products can be designed to be durable and resistant to various environmental factors. This makes them suitable for applications where products need to withstand challenging conditions, such as outdoor exposure or heavy use100.
Thermoforming and thermoformers are integral components of modern manufacturing, shaping a diverse array of products across industries. From its definition to the intricacies of the process and its wide-ranging applications, we hope this comprehensive guide has provided insight into the world of thermoforming. We highlighted the significance of creating innovative and functional products that enhance our daily lives.
Choose Ready Made Plastics
Choosing the right thermoplastic material is crucial for successful thermoforming because different plastics offer different properties and advantages. Before choosing a specific material, consider the requirements of your application, including mechanical properties, chemical resistance, and environmental factors. Testing and prototyping with different materials can help ensure the chosen plastic meets the specific needs of your thermoforming project.
It’s crucial to discuss your exact needs with the manufacturer when thermoforming that fits these requirements in order to make sure that the material you’ve selected complies with all applicable laws and regulations. Furthermore, certification compliance may be significant based on the application and sector.
Although Ready Made Plastics provides these benefits and these different applications, it’s crucial to thoroughly evaluate your needs and take these into account to make sure that the plastic trays from Ready Made Plastics satisfy them. Custom plastic trays may be a preferable option if personalization is important, even though they may be more expensive. For more information, check out Ready Made Plastics. We have many options for you to choose your perfect thermoforming plastic trays. And if you need something custom-made, we can ensure you get the perfect fit.