Understanding the Martindale Pilling Tester: The Key to Reliable Fabric Durability Assessment
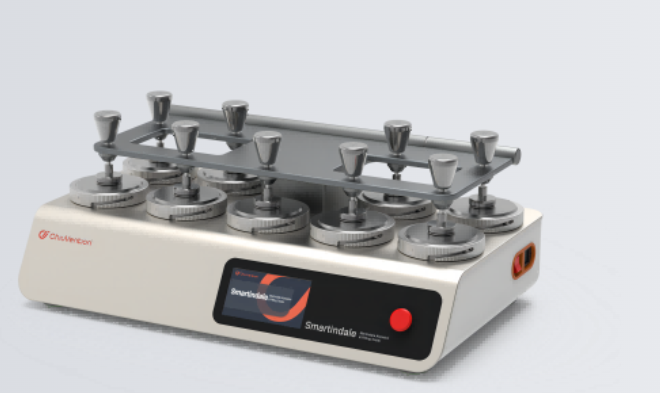
In the textile industry, product quality and performance are not just differentiators—they are requirements. One of the most crucial aspects of fabric quality is its resistance to pilling. Pilling refers to the formation of small, unsightly fiber balls on the surface of fabrics due to abrasion during wear or laundering. For textile manufacturers, designers, and quality assurance professionals, measuring this characteristic accurately is essential. This is where the Martindale pilling tester comes into play.
What is the Martindale Pilling Tester?
The Martindale pilling tester is a specialized instrument used to evaluate the resistance of textiles to pilling and abrasion. Named after Dr. Martindale, who designed the original method, this tester is now considered an international benchmark for assessing fabric durability.
In a standard test, circular fabric samples are subjected to controlled rubbing motion under a defined pressure using a standard abrasive or fabric. After a specified number of cycles, the tested samples are visually inspected and graded based on the extent of pilling.
This method simulates real-world wear conditions and provides a reproducible and reliable indication of how a fabric will perform over time, especially in garments, upholstery, and industrial textiles.
See also: Why Fintech Apps Need Gamification to Drive User Behavior
How the Martindale Tester Works
The core of the pilling Martindale process involves several key components:
- Sample Holders: Circular pieces of fabric are mounted onto the sample holders.
- Abrasion Table: A fabric or standard abradant is placed on the test bed.
- Lissajous Motion: The tester creates a complex oscillating motion called a Lissajous pattern, which ensures multi-directional abrasion.
- Controlled Pressure: The samples are rubbed under uniform pressure to replicate wear.
- Cycle Counting: The number of abrasion cycles is pre-set according to standards such as ISO 12945-2 or ASTM D4970.
After the test, pilling is evaluated against a set of visual standards ranging from Grade 5 (no pilling) to Grade 1 (severe pilling).
Importance of the Martindale Pilling Tester in Textile Quality Control
The Martindale pilling tester plays a pivotal role in fabric R&D, manufacturing, and quality control. Here’s why:
- Objective Evaluation: It provides an objective and standardized method for determining pilling resistance.
- Predictive Performance: It helps predict how fabrics will perform during end-use, reducing customer complaints and returns.
- Global Standardization: It complies with international standards, making it ideal for companies selling to global markets.
- Material Comparison: It aids in comparing different fabrics, blends, or finishing processes to optimize textile formulations.
Applications Across the Textile Industry
The pilling Martindale method is widely adopted across various segments:
- Apparel Manufacturing: Garment producers use the Martindale test to ensure their fabrics maintain appearance over time.
- Home Textiles: Upholstery, curtains, and bed linens are evaluated for long-term use and washing resistance.
- Automotive Interiors: Seats and panels in vehicles undergo testing for abrasion and pilling resistance to maintain aesthetics and durability.
- Technical Textiles: Workwear, performance gear, and protective fabrics are tested to comply with strict industrial standards.
Testing Standards Associated with Martindale
To ensure consistency and comparability of results, several international testing standards are associated with the Martindale fabric test. The most notable include:
- ISO 12945-2: This international standard specifies a method for determining the pilling resistance of fabrics using the Martindale method.
- ASTM D4970 / D4970M: This is the standard test method for pilling resistance and other related surface changes of textile fabrics, particularly in the U.S.
- BS 3424 & BS 5690: British standards also integrate the Martindale methodology for textile testing.
Each of these standards outlines precise sample sizes, cycle counts, grading scales, and testing environments to ensure repeatability.
Key Features to Look for in a Martindale Pilling Tester
When investing in a Martindale pilling tester, procurement specialists and quality control engineers should consider:
- Number of Stations: Common configurations include 4, 6, or 8 stations to accommodate high-throughput testing.
- User Interface: Modern machines come with touchscreen controls and programmable test parameters.
- Compliance Certifications: Ensure the machine is compliant with ISO, ASTM, and other relevant standards.
- Accessories: Look for sample holders, abradants, foam pads, and visual standards included in the package.
- Data Output: Digital data logging and report generation features are crucial for quality audits and R&D analysis.
Differences Between Martindale and Other Abrasion Tests
While the Martindale fabric test is widely used, it is important to distinguish it from other methods such as the Wyzenbeek test, particularly when targeting specific markets or applications.
Feature | Martindale Pilling Test | Wyzenbeek Test |
Motion | Lissajous oscillation | Back-and-forth motion |
Direction | Multi-directional | Unidirectional |
Common in | Europe, Asia | North America |
Suitable for | Apparel, upholstery | Upholstery, contract fabrics |
Test Standards | ISO, ASTM D4970 | ASTM D4157 |
Understanding these differences helps in selecting the most suitable test based on client needs or regional compliance.
How to Interpret Pilling Test Results
The evaluation of pilling in the Martindale test is usually done visually by comparing the tested fabric samples to standard rating images. The results are generally classified as:
- Grade 5: No visible pilling
- Grade 4: Slight pilling
- Grade 3: Moderate pilling
- Grade 2: Considerable pilling
- Grade 1: Severe pilling
Testers often conduct this evaluation after set intervals, such as 1,000, 5,000, or 10,000 cycles, depending on the fabric type and testing standard. Multiple samples are tested to ensure statistical relevance.
Best Practices for Conducting the Martindale Pilling Test
To ensure consistency and accuracy, labs and production teams should follow these best practices:
- Condition Samples Properly: Condition the fabric at 21°C ±1°C and 65% ±2% RH for at least 24 hours before testing.
- Use Standard Abradants: Always use certified abradants and foam inserts as prescribed by the standard.
- Calibrate Equipment: Regular calibration of the tester ensures that pressure, motion, and cycle count are accurate.
- Train Operators: Technicians must be trained to assess pilling visually, as subjective evaluation can vary.
- Document Everything: Maintain detailed records of test parameters, cycles, and evaluation results for traceability.
Common Challenges in Pilling Testing
Even with standardized equipment, challenges can arise:
- Subjectivity in Grading: Human error in visual assessment can lead to inconsistent results.
- Abradant Wear: Worn-out abradants can reduce the severity of abrasion, skewing results.
- Sample Variability: Inconsistent sample cutting or preparation can lead to non-reproducible outcomes.
- Environmental Fluctuations: Variations in temperature and humidity can influence fabric behavior.
Investing in digital imaging software or automated grading systems can help overcome some of these limitations.
Future Trends in Fabric Pilling Testing
As sustainability and performance textiles gain importance, the pilling Martindale method is evolving:
- Digital Evaluation: Computer vision and AI-based image analysis are being integrated to provide objective grading.
- Sustainable Materials: Testing is being adapted for biodegradable, recycled, and performance-enhanced fibers.
- Automated Reporting: Cloud-based data systems now allow global teams to access test results in real time.
- Customization: Manufacturers are offering custom Martindale testers tailored to niche textile applications.
These advancements reflect the growing complexity and innovation in the textile testing ecosystem.
Conclusion
The Martindale pilling tester remains a cornerstone of fabric durability testing, ensuring textile products meet consumer expectations and industry standards. By simulating real-world wear conditions through a standardized methodology, it provides vital insights into material performance. Whether you’re producing apparel, home furnishings, or technical textiles, adopting the pilling Martindale method helps uphold quality, reduce returns, and strengthen brand trust.
For professionals seeking to invest in or better understand this testing method, mastering the martindale fabric test is essential. With the right knowledge, equipment, and execution, this test can be a game-changer for textile innovation and quality assurance.
For more information on textile testing methods/standards
or textile testing machine-TESTEX textile textile testing machines, contact us:
What’s App: +86 180 2511 4082
Tel: +86 769 2329 4842
Fax: +86 769 2329 4860
Email: sales@tes.hk