Tips for Designing High Voltage and Advanced PCBs
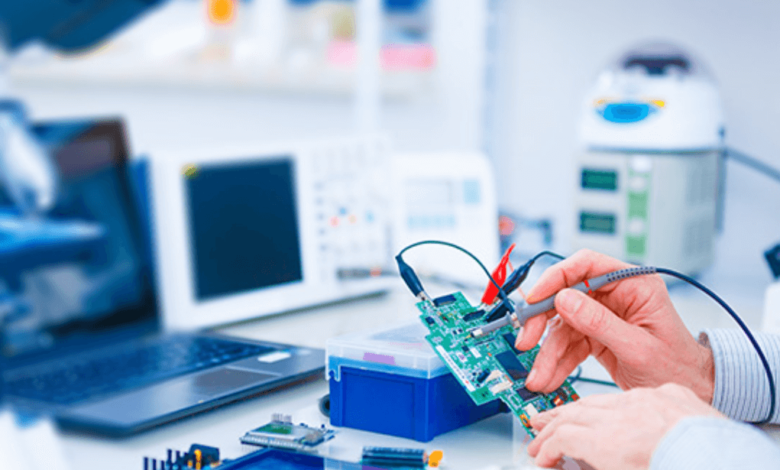
In today’s rapidly evolving electronics landscape, the demand for complex and reliable printed circuit boards (PCBs) is higher than ever. Engineers and product developers face the dual challenge of designing compact circuits that handle high voltage safely and perform flawlessly in critical industries like telecommunications, aerospace, and robotics. Whether you’re designing a high-speed communication device or a control system for automation, understanding the fundamentals and intricacies of high voltage PCB design is key to success.
Manufacturers like Global Well PCBA are meeting these challenges with cutting-edge fabrication techniques, specialized materials, and industry-grade expertise. In this article, we’ll explore essential tips and best practices for designing high voltage PCBs and other advanced circuit boards, including Rigid-Flex and High Frequency PCBs.
1. Understand the Application Requirements
Before starting any PCB design, it’s crucial to define your application and its electrical and mechanical demands. High voltage PCBs are typically used in systems that exceed 100V, such as:
- Power supplies
- Electric vehicles
- Industrial machinery
- Renewable energy systems
- Robotic arms and controllers
The application determines the choice of materials, spacing, insulation, and safety requirements. A robotics system, for example, might require a compact, flexible design with strong signal integrity and electromagnetic compatibility (EMC).
See also: Why Fintech Startups Are Prioritizing Mobile First Experiences
2. Maintain Adequate Clearance and Creepage
When dealing with high voltage, ensuring sufficient spacing between conductive elements is critical. Two key parameters are:
- Clearance – the shortest distance through air between two conductors
- Creepage – the shortest distance along the surface of the board between two conductors
Failure to maintain these distances can lead to arcing, dielectric breakdown, or short circuits. These standards are defined in IPC-2221 and vary depending on voltage level, pollution degree, and materials used.
Tip: For voltages above 300V, increase spacing conservatively, considering both internal and external layers of the PCB.
3. Select the Right Substrate Material
The material used in your PCB plays a major role in its performance. While standard FR-4 may be suitable for low-voltage boards, high voltage and high frequency designs often require advanced materials such as:
- Rogers laminates – known for their low dielectric loss and high thermal stability
- Polyimide – flexible and thermally stable, ideal for Rigid-Flex PCBs
- Ceramic-filled PTFE – excellent for RF and microwave circuits
These materials enhance voltage insulation, minimize signal loss, and improve thermal management, especially in telecommunications and aerospace applications.
4. Use Rigid-Flex Designs for Compact and Complex Applications
Rigid-Flex PCBs combine the benefits of both rigid and flexible substrates. They are ideal for applications where space constraints and movement are factors, such as robotics, drones, and wearable medical devices.
Advantages of Rigid-Flex PCBs:
- Reduced size and weight
- Fewer connectors and solder joints
- Better shock and vibration resistance
- Streamlined assembly processes
High-quality Rigid-Flex PCB solutions, like those from globalwellpcba.com, offer significant performance advantages for advanced tech applications.
5. Consider High Frequency PCB Requirements
In applications like radar systems, satellite communications, and 5G base stations, signal integrity at high frequencies is paramount. High Frequency PCBs are specifically designed to handle gigahertz-level signals with minimal interference.
Design tips for High Frequency PCBs:
- Use controlled impedance traces
- Minimize dielectric loss by selecting low-loss substrates
- Avoid sharp trace corners and stubs to reduce signal reflections
- Ground planes should be continuous and well-isolated
Even slight design missteps can result in signal degradation, making it essential to partner with experienced PCB manufacturers who specialize in high-speed and RF PCB design.
6. Optimize the PCB Layout for Thermal Management
High voltage PCBs often generate significant heat, especially when used in power electronics or motor control systems. Effective thermal management can prevent damage, extend lifespan, and ensure safe operation.
Key considerations:
- Add thermal vias and heat sinks
- Distribute power and ground planes efficiently
- Use thicker copper for power-carrying traces
- Keep high-power components isolated from sensitive areas
Thermal simulation tools can also help during the layout phase to predict and address hot spots early.
7. Improve Reliability Through Conformal Coating
To protect high voltage and high frequency PCBs from moisture, dust, and other environmental hazards, many engineers apply a conformal coating. This thin polymeric layer enhances dielectric strength and prevents arcing or corrosion.
Popular coatings include:
- Acrylics (easy to apply and repair)
- Polyurethanes (great chemical resistance)
- Silicone (for extreme temperature tolerance)
Conformal coatings are especially useful in outdoor telecom systems and industrial automation where harsh conditions are common.
8. Perform Rigorous Testing and Validation
High voltage and advanced PCBs must undergo strict testing to ensure safety and reliability. Testing methods include:
- Dielectric withstand testing (HiPot) – to verify insulation resistance
- Impedance testing – to confirm signal integrity
- X-ray inspection – for BGA and multilayer board verification
- Thermal cycling – to simulate real-world operating conditions
Partnering with a manufacturing expert like Global Well PCBA ensures your boards meet all necessary industry standards, such as UL, RoHS, and ISO certifications.
9. Collaborate with an Experienced PCB Manufacturer
Designing high voltage and specialized PCBs is not a solo journey. It requires deep collaboration with a trusted PCB fabricator who understands your technical needs, time constraints, and industry-specific requirements.
A manufacturer with proven expertise in advanced PCBs will offer:
- Design-for-manufacturing (DFM) guidance
- Material selection support
- Custom prototyping and small-batch production
- High-layer count, HDI, and Rigid-Flex fabrication
- Component sourcing and turnkey assembly
With the help of an expert like Global Well PCBA, your design can move from concept to production with confidence and quality assurance.
Conclusion
High voltage PCB design and other advanced circuit board technologies are driving innovation in telecommunications, robotics, energy, and beyond. As electronics continue to evolve, the need for precision, safety, and reliability becomes even more critical. By following best practices in layout, material selection, thermal management, and testing, engineers can develop high-performance boards that stand up to the most demanding applications.
Whether you’re working on a cutting-edge robotic controller or a power conversion unit, collaborating with seasoned manufacturers like Global Well PCBA ensures your design is optimized from the ground up. Their technical capabilities, global reach, and commitment to quality make them a reliable partner for your next high voltage or advanced PCB project.