Understanding Cold Solder: Causes, Effects, and Prevention in PCB Assembly
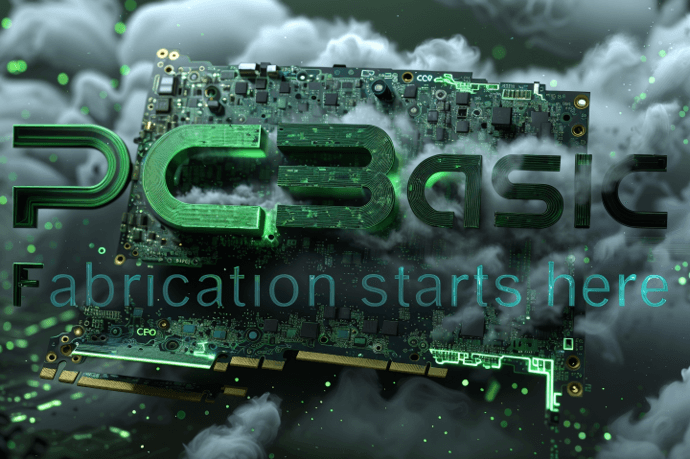
Soldering is a critical step in the assembly of Printed Circuit Boards (PCBs), ensuring that electrical components are securely connected to the board. While soldering is a relatively straightforward process, issues such as cold solder joints can lead to significant problems, including unreliable connections and potential circuit failure. In this article, we’ll explore what cold solder is, its causes, effects on PCB performance, and how to prevent it.
What is Cold Solder?
A cold solder joint refers to a solder connection that has not been properly melted or bonded. This usually results in a weak, unreliable, or intermittent connection between the component lead and the PCB. The primary indicator of a cold solder joint is the lack of a smooth, shiny solder fillet that should form around the joint when the solder is correctly heated and flows.
In an ideal soldering process, the solder should melt and flow into the joint, creating a strong, electrically conductive bond. However, when the solder fails to melt completely, or when the soldering iron doesn’t reach the right temperature for long enough, the result is a cold solder joint.
See also: The Art of Embossing: Techniques and Tips for Beautiful Results
Causes of Cold Solder Joints
There are several factors that can lead to the formation of cold solder joints during PCB assembly:
1. Insufficient Heating
One of the most common causes of cold solder joints is insufficient heating of either the PCB pad or the component lead. If the soldering iron doesn’t stay in contact with the joint long enough or doesn’t provide enough heat, the solder will not fully melt and flow into the joint. This leads to weak, unreliable connections.
2. Low-Quality Solder
The quality of the solder material used can also contribute to cold solder joints. Solder that contains impurities or is of low quality may not melt or flow as easily, which can result in an incomplete or cold joint.
3. Incorrect Soldering Iron Temperature
If the soldering iron temperature is too low, the solder may not melt correctly, while excessive heat can damage sensitive components. The ideal temperature for most lead-based solders is between 350°C to 375°C, but this may vary depending on the specific solder alloy.
4. Poor Soldering Technique
Improper technique, such as moving the soldering iron too quickly or not applying enough pressure, can also result in cold solder joints. The solder must be applied evenly around the entire joint, and the components must be held in place until the solder solidifies.
5. Dirty Components or PCB Pads
Oxidation, dirt, or residue on the component leads or PCB pads can prevent the solder from flowing correctly. Contaminants on the surfaces can interfere with the solder’s ability to form a strong bond, leading to cold solder joints.
6. Excessive Flux Residue
While flux is necessary for soldering, excessive or improperly cleaned flux can prevent solder from properly adhering to the joint, causing an incomplete bond that leads to cold soldering.
Effects of Cold Solder Joints on PCBs
Cold solder joints can cause several issues that affect the performance, reliability, and longevity of PCBs:
1. Electrical Failures
A cold solder joint often creates an intermittent or weak electrical connection. This can lead to unreliable circuit behavior, erratic performance, or complete failure of the component. This is particularly problematic in high-frequency or high-power circuits, where even minor disruptions in the electrical path can have a significant impact.
2. Mechanical Instability
In addition to electrical problems, cold solder joints can result in poor mechanical connections. Components may become loose or detached over time due to mechanical stress or vibrations, leading to further failure. This is especially critical in automotive, industrial, or military applications where equipment is exposed to constant movement and stress.
3. Reduced Lifespan
Cold solder joints are typically weaker and more prone to wear over time, especially in environments subject to thermal cycling or mechanical strain. Over time, these joints can degrade further, leading to eventual circuit failure.
4. Difficulty in Troubleshooting
Cold solder joints are often difficult to detect visually because they may not present obvious signs of failure immediately. This can make troubleshooting more challenging, especially in complex boards with many components. Cold solder joints can result in phantom issues that only appear intermittently, which can be frustrating for engineers during the testing phase.
How to Identify Cold Solder Joints
Detecting cold solder joints can be tricky because the problem might not be obvious at first glance. However, there are several ways to identify them:
1. Visual Inspection
A cold solder joint often appears dull, grainy, or cracked, rather than smooth and shiny. A shiny, smooth finish is usually a sign of a good, well-formed solder joint. Additionally, a cold joint might have a ring around it, which indicates that the solder has not fully flowed or bonded to the joint.
2. X-ray Inspection
In complex PCBs or multi-layered boards, X-ray inspection may be required to detect cold solder joints, especially in areas that are not easily visible or accessible.
3. Continuity Testing
Using a multimeter to test for continuity across joints can help identify potential cold solder connections. An inconsistent or interrupted signal indicates an unreliable joint.
4. Mechanical Testing
Gently tapping or applying pressure to a joint can sometimes reveal cold solder joints, as they may move slightly or crack under pressure.
Preventing Cold Solder Joints
Preventing cold solder joints requires attention to detail and careful control of the soldering process. Here are some tips to minimize the risk:
1. Proper Soldering Iron Temperature
Always ensure that your soldering iron is set to the correct temperature, typically between 350°C to 375°C for lead-based solder. Use a thermometer or soldering iron with a temperature control feature to ensure consistent heat.
2. Adequate Heating Time
Spend enough time heating both the PCB pad and the component lead to ensure proper solder flow. Avoid rushing the process, as it can result in incomplete joints.
3. Use High-Quality Solder
Opt for high-quality solder that is compatible with your components and PCB material. Lead-free solder requires slightly higher temperatures than traditional lead-based solder, so be sure to adjust accordingly.
4. Clean Components and Pads
Ensure that the components and PCB pads are free from dirt, oxidation, and flux residues before soldering. Use a PCB cleaner or isopropyl alcohol to clean the pads and leads.
5. Proper Soldering Technique
Maintain a steady hand and ensure that the soldering iron tip is in full contact with both the component lead and the PCB pad for the appropriate amount of time. Avoid moving the soldering iron too quickly or too erratically.
Conclusion
Cold solder joints are a common but avoidable issue in PCB assembly. Understanding the causes, identifying the symptoms, and taking preventive measures can significantly improve the quality and reliability of your PCB assembly process. By ensuring proper soldering techniques, correct temperatures, and clean surfaces, you can avoid the risks associated with cold solder joints and improve the overall performance and longevity of your electronic products.