Understanding the Pigging Manifold: A Key Component in Efficient Pipeline Systems
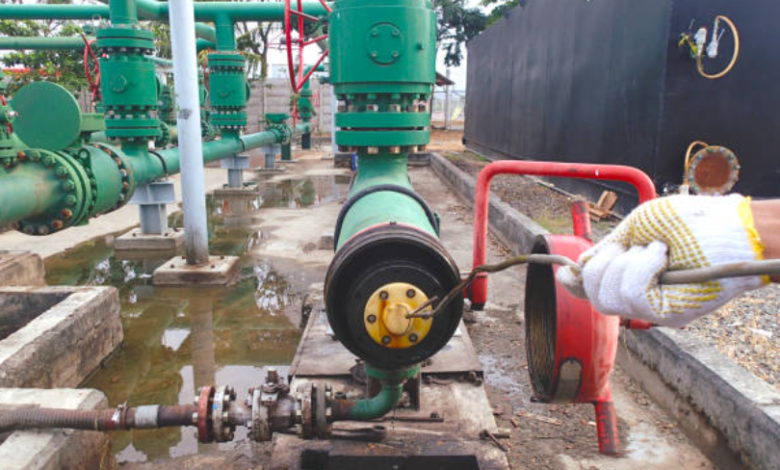
In industries that rely heavily on fluid transportation—like oil & gas, food and beverage, chemicals, cosmetics, and pharmaceuticals—efficiency, hygiene, and waste reduction are constant priorities. Among the many technologies that support these goals, pigging systems play a vital role. One essential component in these systems, often underestimated, is the pigging manifold.
A pigging manifold is more than just a network of pipes—it is the brain and backbone of an automated pigging process. It enables the routing of pigs, the direction of flow, and the integration of multiple pipelines or production lines into a unified cleaning or product recovery system.
This article explores what a pigging manifold is, how it functions, its types, benefits, and best practices for selection and integration into existing infrastructure.
What Is a Pigging Manifold?
A pigging manifold is a specially designed piping system equipped with multiple valves, connections, and routes that guide pigging tools (or pigs) through pipelines for tasks such as cleaning, product recovery, or separation.
Unlike simple T- or Y-junctions, a pigging manifold manages complex routing between multiple pipelines, allowing the pig to enter, exit, or switch paths as required. It acts as a control hub that coordinates pigging operations with minimal human intervention and without disrupting normal pipeline activity.
Manifolds are especially important in facilities with:
- Multiple product lines
- Frequent product changeovers
- Branching or looped pipeline layouts
- High hygiene standards
- Limited downtime availability
See also: Discover the Future of Pond Filtration with Swimming Pond Hoover Technology
Types of Pigging Manifolds
Different applications require different pigging manifold configurations. The most common types include:
1. Manual Manifolds
These systems use manually operated valves. While cost-effective and simple, they are best suited for low-frequency pigging where full automation isn’t necessary.
2. Automated Manifolds
Controlled via PLC or SCADA systems, these use actuated valves to direct pigs and control flow automatically. They’re ideal for high-volume or continuous processing environments where human error must be minimized.
3. Hygienic Manifolds
Made of stainless steel and designed according to 3-A or EHEDG standards, these manifolds are used in food, pharmaceutical, and cosmetic production. Their polished internal surfaces prevent bacterial growth and product buildup.
4. Multi-Line Manifolds
These are designed to connect multiple lines—either from different sources to one destination (or vice versa). Multi-line pigging manifolds are commonly found in bottling plants or chemical blending facilities.
Advantages of Using a Pigging Manifold
Implementing a pigging manifold in your process pipeline system brings several important advantages:
🟢 Increased Productivity
Automated pigging manifolds significantly reduce downtime between production runs, especially during product changeovers. What once took hours can now be done in minutes.
🟢 Reduced Product Waste
Pigs push residual product through the pipeline to the next process stage, reducing waste. This is particularly important for expensive or viscous materials like cosmetics, dairy, syrups, and resins.
🟢 Improved Hygiene
Especially in sanitary industries, a hygienic pigging manifold minimizes the risk of cross-contamination and supports stringent cleaning protocols.
🟢 Space Optimization
Instead of using multiple pipeline systems or manual diversions, a manifold provides a compact, centralized control point that saves space and infrastructure costs.
🟢 Process Automation
Pigging manifolds can be fully integrated into existing automated process systems, providing real-time monitoring, control, and safety interlocks.
Key Components of a Pigging Manifold
A functional pigging manifold typically includes:
- Valves (manual or automated) for controlling the direction of flow
- Sensors to detect pig movement or position
- Actuators for automated valve operations
- Launchers and Receivers to introduce or remove pigs from the system
- Control Panel or PLC Interface to manage the sequencing of pigging and cleaning cycles
Some advanced manifolds also incorporate:
- Magnetic detectors for pig location tracking
- Pressure regulators for safe pig propulsion
- Pigging pig buffers for managing multiple pigs in the system
Applications of Pigging Manifolds by Industry
🛢️ Oil and Gas
Used to switch between different product pipelines, manage batch separation, or perform pipeline integrity cleaning.
🧴 Cosmetics and Personal Care
Manages the cleaning and product switching between different viscous products like creams, lotions, and gels.
🥫 Food and Beverage
Used in dairy, soft drinks, and sauce production to clean lines between product batches while maximizing yield.
💊 Pharmaceuticals
Manifolds in this sector help maintain GMP compliance and ensure that high-purity product batches remain uncontaminated.
Best Practices for Designing a Pigging Manifold System
To make the most of your pigging manifold, consider the following tips:
- Assess All Flow Paths: Map every potential product route in the facility and determine which can be serviced by the same manifold.
- Choose Appropriate Materials: In sanitary applications, use 316L stainless steel with polished surfaces and sanitary fittings.
- Account for Future Expansion: Design manifolds with spare ports or valves to accommodate future production lines.
- Automate Where Possible: PLC-controlled systems reduce errors and improve safety.
- Plan for Maintenance: Include drain ports, pig launchers, and access points for inspection and servicing.
Future Trends in Pigging Manifold Systems
As processing industries shift toward smart manufacturing, the pigging manifold is evolving too:
- Smart Valve Control: With feedback-enabled actuators and IIoT sensors, real-time diagnostics and predictive maintenance are becoming common.
- CIP Integration: Full cleaning cycles with no manual intervention—perfect for 24/7 operations.
- Compact Modular Designs: These systems can be adapted to fit into small spaces while handling complex routing.
- Green Manufacturing Compliance: Manifolds are helping reduce water, chemical, and energy usage in line with sustainability targets.
Conclusion
The pigging manifold might not always take center stage in pipeline conversations, but its value is undeniable. It acts as the command center for product transfer, cleaning, and switching—enabling manufacturers to run cleaner, leaner, and more efficient operations.
Whether you’re producing beverages, cosmetics, or petrochemicals, investing in the right pigging manifold setup can transform your process flow, reduce costs, and enhance product integrity. In today’s highly competitive and regulation-driven world, adopting intelligent pigging manifold solutions is not just good practice—it’s essential.