Precision CNC Machining
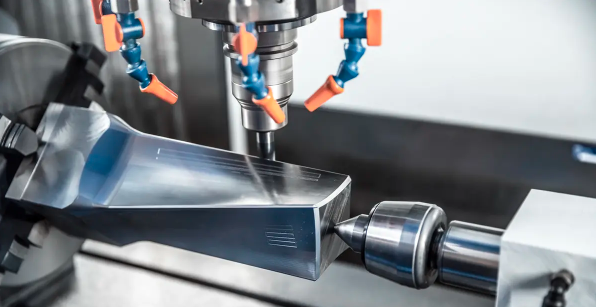
Introduction
In today’s manufacturing world precision cnc machining stands as one of the most critical and transformative technologies. From aerospace components to intricate medical devices, this technique enables manufacturers to produce parts with exceptional accuracy and repeatability. This method ensures every component is made to exact specifications, minimizing human error and enhancing productivity.
Core Concept
Precision CNC machining involves the use of pre-programmed software to control tools such as mills, lathes, grinders, and routers. The software guides each step of the cutting, drilling, or shaping process, allowing for tight tolerances and consistent results across large volumes.
The precision aspect comes from the machine’s ability to hold dimensions within a few microns, ensuring uniformity in each production run. This level of control is essential when producing complex parts for industries that demand high reliability.
Key Components
A typical precision CNC machining setup includes three main components: the machine, the control unit, and the cutting tool. The machine moves along multiple axes (usually X, Y, and Z) to shape the material. The control unit processes the digital instructions, translating them into movements. The cutting tool does the actual shaping, often made of high-speed steel or carbide.
Some CNC machining centres are 5-axis, offering even more flexibility and capability to produce intricate geometries.
Read also: Sanctions Screening Compliance: A Key to Business Integrity
Materials Used
Manufacturers can use this process on metals like aluminum, titanium, stainless steel, and brass, as well as plastics, composites, and even ceramics.
Each material behaves differently under machining conditions, and CNC programming is adjusted accordingly. For example, titanium requires slower cutting speeds and more rigid setups due to its toughness, while aluminum allows for faster processing due to its softness.
Applications
The applications of precision CNC machining are vast. In the aerospace industry, it’s used to create critical components like turbine blades, engine housings, and structural parts. These pieces must adhere to strict safety and performance standards.
In the medical field, CNC machines produce surgical instruments, implants, and diagnostic equipment components. Their ability to maintain accuracy ensures patient safety and regulatory compliance.
Automotive industries use CNC machining for engine blocks, transmission parts, and custom prototypes. Consumer electronics, robotics, military equipment, and energy sectors also rely heavily on precision CNC services.
Tolerances and Accuracy
In precision CNC machining, tolerances refer to the allowable deviation from a specified measurement. These can be as tight as ±0.001 inches or even tighter, depending on the application. Maintaining such tight tolerances is crucial when the part’s function relies on exact alignment or fit with other components.
Machinists use tools like coordinate measuring machines (CMM), laser scanners, and micrometers to verify that each part meets the desired specifications. The result is consistent performance and quality.
Benefits
One major benefit of precision CNC machining is its ability to reduce waste. By following exact designs and using materials efficiently, companies save both time and resources. It also increases production speed, as the automation allows for round-the-clock operation without compromising quality.
Moreover, CNC machining is extremely scalable. Whether you need one prototype or a run of thousands, the process can be adjusted to meet the demand without sacrificing precision.
Challenges
While precision CNC machining offers numerous advantages, it is not without challenges. The initial setup cost can be high, especially when purchasing advanced multi-axis machines or hiring skilled operators. Additionally, programming errors or tool wear can lead to defects, so careful monitoring and regular maintenance are crucial.
Another challenge lies in material behavior. Some materials may warp or react during machining, which can compromise accuracy. To mitigate this, manufacturers must understand material properties and adjust tool paths, speeds, and feeds accordingly.
Industry Trends
Modern developments in precision CNC machining are being driven by automation, AI integration, and IoT connectivity. Machines are now capable of self-monitoring, adjusting feeds and speeds based on cutting conditions, and alerting operators to potential issues.
Another rising trend is the use of hybrid manufacturing systems that combine additive and subtractive processes. These systems allow for complex geometries that were once impossible with machining alone. Cloud-based platforms also offer remote access and real-time monitoring, improving productivity and decision-making.
Choosing a CNC Partner
Selecting the right precision CNC machining partner is vital for success. Companies should look for shops with experience in their specific industry, access to advanced machinery, and strict quality control measures. Certifications like ISO 9001 or AS9100 are indicators of a commitment to quality and compliance.
Communication is another key factor. A good CNC provider will collaborate with clients, offering design suggestions, material advice, and rapid prototyping to improve part performance and manufacturability.
Environmental Impact
With growing emphasis on sustainability, precision CNC machining is evolving to reduce environmental impact. Efficient chip removal systems, coolant recycling, and the use of eco-friendly materials all contribute to greener manufacturing.
Future Outlook
The future of precision CNC machining looks promising. As technology continues to advance, machines will become even more intelligent, autonomous, and energy-efficient. With the increasing demand for customized, high-performance components, precision CNC will remain a pillar of modern manufacturing.
Integration with digital twins, real-time data analytics, and AI-driven design optimization will revolutionize how parts are made, reducing lead times and enhancing product innovation.
Conclusion
Precision CNC machining has reshaped the manufacturing landscape. Its ability to deliver exact, repeatable parts across a range of materials and industries makes it an indispensable tool. Despite the challenges, its advantages in accuracy, scalability, and efficiency ensure its relevance in today’s competitive environment. As industries evolve, so will CNC technology, continuing to set new standards in quality and innovation.