Exploring Vacuum Casting Services: Precision Replication for Modern Manufacturing
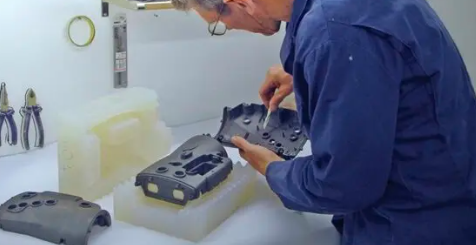
Introduction
In the fast-evolving world of manufacturing Vacuum Casting Services have emerged as a preferred solution for creating high-quality prototypes and low-volume production parts. This technique bridges the gap between 3D printing and injection molding by offering a flexible, cost-effective, and highly precise method for duplicating parts. Whether used for visual models, functional testing, or end-use components, vacuum casting delivers accuracy, repeatability, and excellent surface finish.
This article explores the vacuum casting process, its benefits, applications, limitations, and why it’s a valuable asset in modern manufacturing environments.
What Is Vacuum Casting?
Once the material cures, the mold is opened, and a precise replica of the master model is extracted.
It is widely used for rapid prototyping, bridge tooling, and short-run manufacturing due to its ability to produce complex geometries with excellent detail and dimensional accuracy.
How the Process Works
Step 1: Master Model Creation
The process starts with a master model, typically produced using high-resolution 3D printing (like SLA or SLS) or CNC machining. The model must have an impeccable surface finish because every detail will be transferred to the mold.
Step 2: Silicone Mold Making
Once the master model is ready, it is placed inside a casting box, and liquid silicone rubber is poured over it.
Step 3: Vacuum Casting
The chosen casting resin is mixed and poured into the silicone mold inside a vacuum chamber. The vacuum removes any trapped air, ensuring a bubble-free and accurate casting. The mold is then left to cure either at room temperature or in a heated oven, depending on the material used.
Materials Used in Vacuum Casting
Vacuum casting supports a wide range of polyurethane-based resins that mimic the properties of standard plastics such as:
- ABS-like resin: For general-purpose parts requiring good toughness.
- Polycarbonate-like resin: For clear parts or lenses.
- Rubber-like resin: For flexible, elastic components.
- Nylon-like resin: For mechanical components that need strength and temperature resistance.
- Flame-retardant or food-safe materials: For specialized applications.
This material versatility makes vacuum casting suitable for both functional and visual prototypes.
Key Advantages of Vacuum Casting Services
1. High-Quality Surface Finish
Thanks to silicone molds, vacuum-cast parts often require little to no post-processing. The molds replicate even the smallest surface textures of the master model.
2. Short Turnaround Time
Compared to injection molding, vacuum casting requires significantly less setup time. Most parts can be delivered in days, making it ideal for fast-moving projects.
3. Cost-Effective for Low Volumes
For short production runs, the low cost of mold creation makes vacuum casting more affordable than traditional tooling, which can be prohibitively expensive.
4. Material Flexibility
Vacuum casting can simulate a wide array of production plastics, allowing manufacturers to test performance, fit, and finish before investing in large-scale tooling.
See also: Magento vs Shopify: Which Platform Is Right for Your eCommerce Business?
Common Applications
- Automotive: For concept parts, housing components, lenses, and ducts.
- Medical Devices: For casings, ergonomic models, and functional testing.
- Consumer Electronics: Prototypes for enclosures, connectors, and soft-touch buttons.
- Industrial Equipment: Rapid iteration of functional parts or ergonomic tools.
- Fashion and Accessories: Replica jewelry, buckles, and wearable tech prototypes.
The ability to create detailed, functional parts quickly makes vacuum casting especially valuable during product development cycles.
Vacuum Casting vs Injection Molding
While both processes produce plastic parts using molds, they serve different purposes:
Feature | Vacuum Casting | Injection Molding |
---|---|---|
Mold Type | Silicone | Metal (steel or aluminum) |
Cost | Low for short runs | High upfront investment |
Lead Time | 5–10 days | Several weeks |
Quantity | 1–100 parts | 1,000+ parts |
Material Range | Polyurethane resins | Engineering-grade plastics |
Limitations of Vacuum Casting
While vacuum casting services offer several advantages, there are also some limitations to consider:
1. Limited Mold Life
Silicone molds degrade over time, especially with complex geometries or high-temperature resins. Most molds can produce 20–25 parts before replacement is needed.
2. Size Constraints
Large parts may require special equipment or assembly from smaller sections.
3. Material Properties
While resins can mimic production plastics, they don’t always offer the same long-term performance characteristics (e.g., UV resistance, chemical stability).
Choosing the Right Vacuum Casting Service Provider
Selecting a professional vacuum casting service provider ensures part accuracy, mold longevity, and overall satisfaction. Here are key factors to consider:
- Experience and Portfolio: Ask for examples of previous work, especially if your part has complex features or material requirements.
Future of Vacuum Casting
With the rise of rapid prototyping and on-demand manufacturing, vacuum casting continues to evolve. Integration with digital manufacturing platforms and advanced resins now allows for even better replication of production-grade parts.
As product development becomes increasingly agile, vacuum casting is becoming indispensable for delivering quick, affordable, and high-fidelity parts.
Conclusion
The ability to replicate intricate details, choose from a range of materials, and achieve production-like quality makes it a preferred technique for many industries.
While it’s not a replacement for mass manufacturing, vacuum casting fills a crucial role in early product development, market testing, and bridge production. By understanding the process, benefits, and limitations, manufacturers and designers can make informed decisions and bring their ideas to life with speed and precision.